In machine manufacturing, in addition to speed and efficiency, safety cannot be ignored. This largely depends on the design concept of the machine, but small things like an improperly fitting part or incorrect positioning within the machine also play a role. Complete safety can therefore be guaranteed by the cooperation of a competent machine manufacturer and a safety technology expert. Zoltán Szalai, project manager of Auware Engineering Kft., Bálint Nizsalócki, company manager of Euchner Magyarország Kft., and service manager Máté Szabó introduce the readers of TechMonitor to the process of reviving a machine that is already being scrapped elsewhere.
What task was the now modernized equipment originally built for?
Zoltán Szalai: The target machine in question, a hydraulic steering servo test device built in 1987, is currently owned by a domestic TIER-1 automotive supplier, but it is considered a real-world traveler. It was originally put into operation in Germany, then transported to Russia, from where it was brought to Hungary last year.
In more than three decades, quite a few creases may have been sewn on the machine.
Zoltán Szalai: In accordance with the original task of the equipment, it tested steering servos manufactured for trucks and buses. In the 80s, the testing process was obviously still dreamed up with analog instruments, which were updated in the 2000s with a modern computerized measurement system, in addition to the installation of separate measurement points. We have been in a business relationship with the customer since 2018, and we were entrusted with the modernization of the test equipment in 2021.
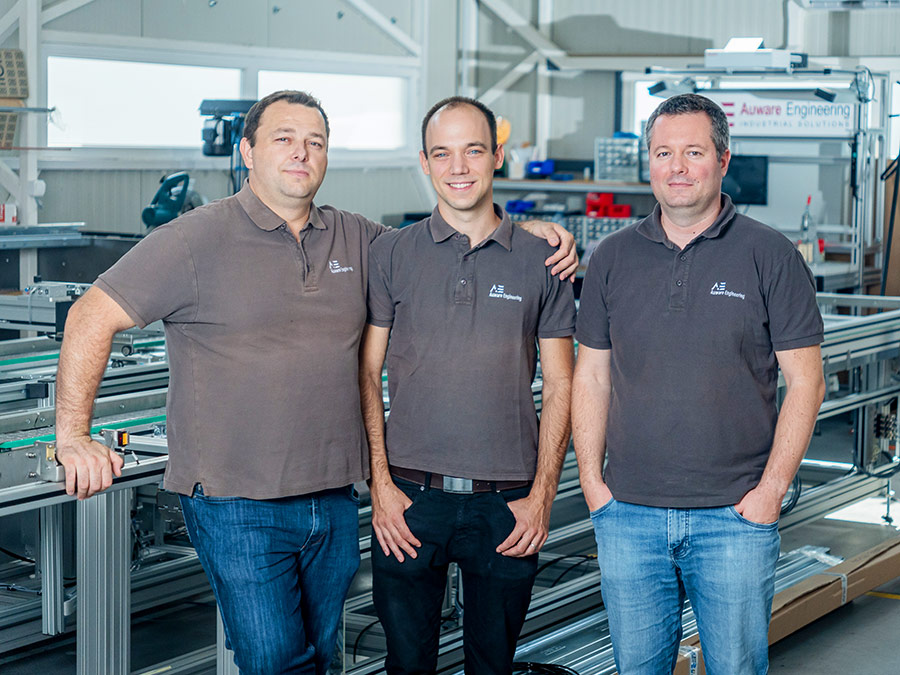
How did you win the assignment?
Zoltán Szalai: Auware Engineering Kft. mainly specializes in writing and maintaining PC- and PLC-based industrial software, but we also offer the construction of new machines and the renovation of old production equipment. We originally performed equipment maintenance for the automotive supplier, but it was also known before them that we also deal with modernization. Several companies were contacted for the task, including the original German manufacturer of the machine, who did not go out of their way to undertake the renovation of the equipment. Our offer was the most attractive, thanks to which the work could start in August 2021, which has now been completed, apart from a few minor details.
What did the modernization of the machine consist of?
Zoltán Szalai: We had to make the equipment CE-compliant, because this was not a consideration during operation in Russia. For the machine to comply with the current standards, we asked for the help of Euchner, who compiled the list of deviations and the risk assessment to achieve CE conformity. We completely replaced the equipment of the control cabinet and installed modern safety technology elements. Euchner controlled what interventions were needed and then performed the validation of the safety program.
Máté Szabó: Euchner primarily deals with the distribution of industrial safety equipment, but we have supplemented this with safety engineering, accident prevention, and EC conformity assessment services. Our partners can be end users or machine manufacturers, with whom we have been in contact since the beginning. Depending on when we are involved in the projects, we can also participate in the design tasks of the equipment. Safety devices are key machine components, the selection of which is mostly decided by the end users. For our part, we are of course happy if Euchner products are included in the machine, but the provision of the service is independent of this. The Euchner MSC safety controller was finally installed in the machine.
Bálint Nizsalócki: It is very important for us to separate sales and service and that our service is truly brand independent. By the way, the launch of the complete machine safety service line was the first in Hungary within the company group.
How did the work go?
Zoltán Szalai: The machine was disassembled and rebuilt at the customer’s site, with such ease that the equipment was not put into operation. The other production lines did not have to be stopped during the work, so production continued uninterrupted. A few surprises hit us during the work. On the back of the machine, for example, there were three hydraulic machine units with rather loud pumps. To reduce noise emissions, the customer would have originally insulated the tanks, but instead placed them in a closed enclosure. The only problem with this was that we replaced the drives originally designed to withstand an operating temperature of 60 ̊C with ones of 50 ̊C, saying that the equipment will operate in an air-conditioned room. However, it was no longer possible to guarantee the drive’s survival when sealed with a tank heated to 50 ̊C, so we installed a thermal protection system.
Máté Szabó: From our point of view, the renovation of the machine was of outstanding importance because Euchner signs the final document of EC conformity, hence we also assume the responsibility for market surveillance. It was therefore very important that we worked with a machine manufacturer that was able to do what we had determined to do, and if we had to look for another solution, he was always ready to negotiate. Thus, in the end, a machine and technical documentation was created that meets the relevant standards, and this can still be considered one of the biggest shortcomings of machine manufacturers.
Bálint Nizsalócki: If there is trust and openness, which was considered natural in the case of Auware Engineering Kft., then we will take over the responsibility from the machine manufacturer.
Zoltán Szalai: Not yet in this work, at that time the association was very fresh, since Auware Engineering Kft. became part of Central European Automation Holding (CEAH) in May 2021. We now have completed and ongoing joint machine building projects with both Automa CZ and Antra ID Kft., so we complement each other perfectly. From a commercial point of view, it also matters a lot that we got to know each other’s clientele.
– Molnár László, TechMonitor